К нам из цеха пришли инженеры и попросили сделать ИТ-систему.
Если вы знакомы со спецификой «суровых производственных мужчин», то знаете, что от них это звучит примерно так же, как «тыквенный смузи и веганский стейк, пожалуйста», — ещё два года назад мы о таком проявлении доверия к ИТ со стороны производства даже мечтать не могли. А тут оказалось, что им нужен инструмент, чтобы контролировать износ сегментов УНРС (установки непрерывной разливки стали), потому что это не только убирает рутину, напрямую влияет на качество продукта — слитков стали, но и снижает потенциальный риск прорыва сегмента с расплавом.
Итак, знакомьтесь, вот один из ручьёв УНРС:
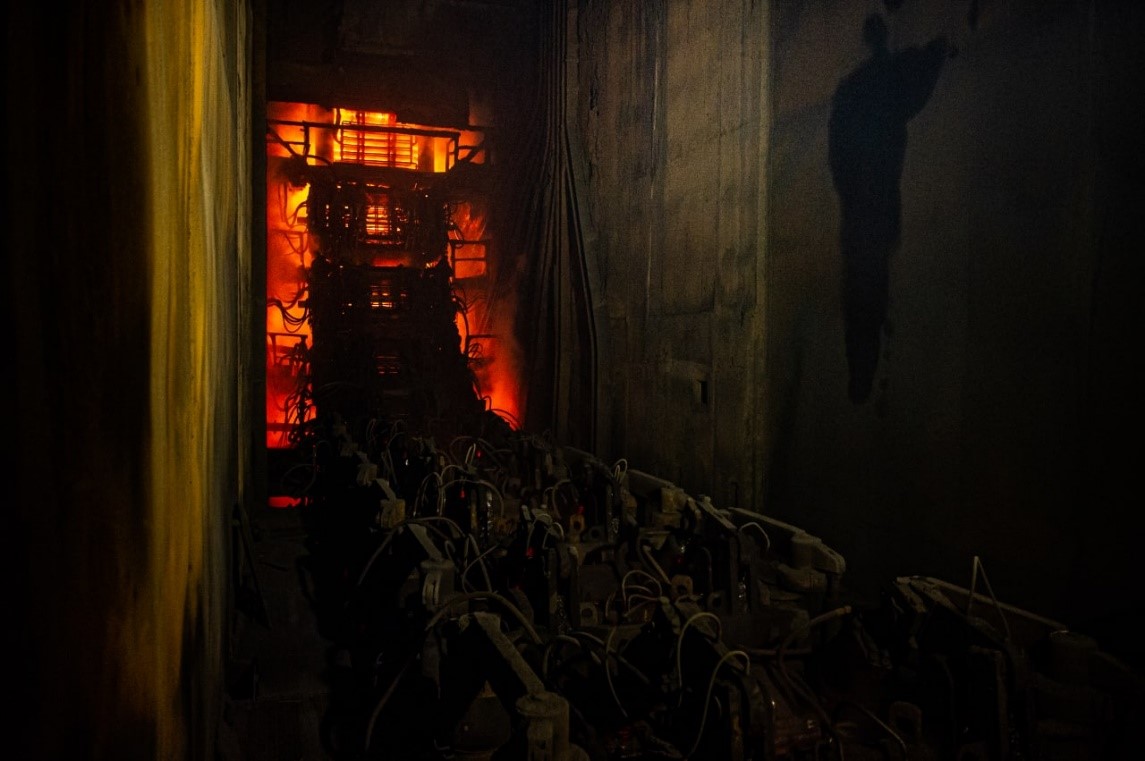
Сверху на УНРС приходит ковш, снизу выпадает огромный слиток стали — сляб. Если вы думаете, что достаточно просто залить сталь из ковша в формочку, то нет. Надо, чтобы всё это равномерно остыло, иначе внутри будут раковины, трещины и другие неприятности. Поэтому процесс такой: сверху буфер, бассейн-накопитель для жидкой стали, дальше каскад сегментов-обработчиков. Сталь проливается вниз, а каждый сегмент охлаждает её. В бассейн подаются ковши с расплавом, которые его наполняют.
Самое опасное в УНРС — не уследить за износом какого-то одного из сегментов, по которому идёт расплав, постепенно превращаясь в сляб. И оказалось, что можно свести такую вероятность к нулю, если избавиться от кучи отдельных бумажных документов и автоматизировать контроль.
Технологи хотели от нас предельно простого работающего решения, чтобы они в каждый момент очень чётко представляли себе статус каждого узла машины. Никакой математики. Никакого дата-майнинга. Никаких нейросетей. Никаких сложных научных исследований.
Сейчас покажу результат.
Читать полностью »